Lidar empowers Autonomous Guided Vehicles (AGVs) and Autonomous Mobile Robots (AMRs) with accurate 3D perception and real-time obstacle detection, ensuring safe navigation while complete unmanned tasks even in dynamic and complex warehouse environments.
With accurate obstacle detection and terrain sensing, lidar-equipped vehicles can navigate complex port & yard environments autonomously, streamlining cargo transportation, and improving overall operational efficiency.
Empowering Success: Stories from Our Customers
ABOUT SEGWAY ROBOTICS AND ITS NOVA CARTER AMR
Segway Robotics is global innovator in short-distance transportation and service robots’ industries. Its Nova Carter is an advanced AMR designed to accelerate the creation and deployment of next-generation robots. It is equipped with Hesai's XT32 lidar that enables 3D sensing, autonomous navigation, and real-time obstacle avoidance.
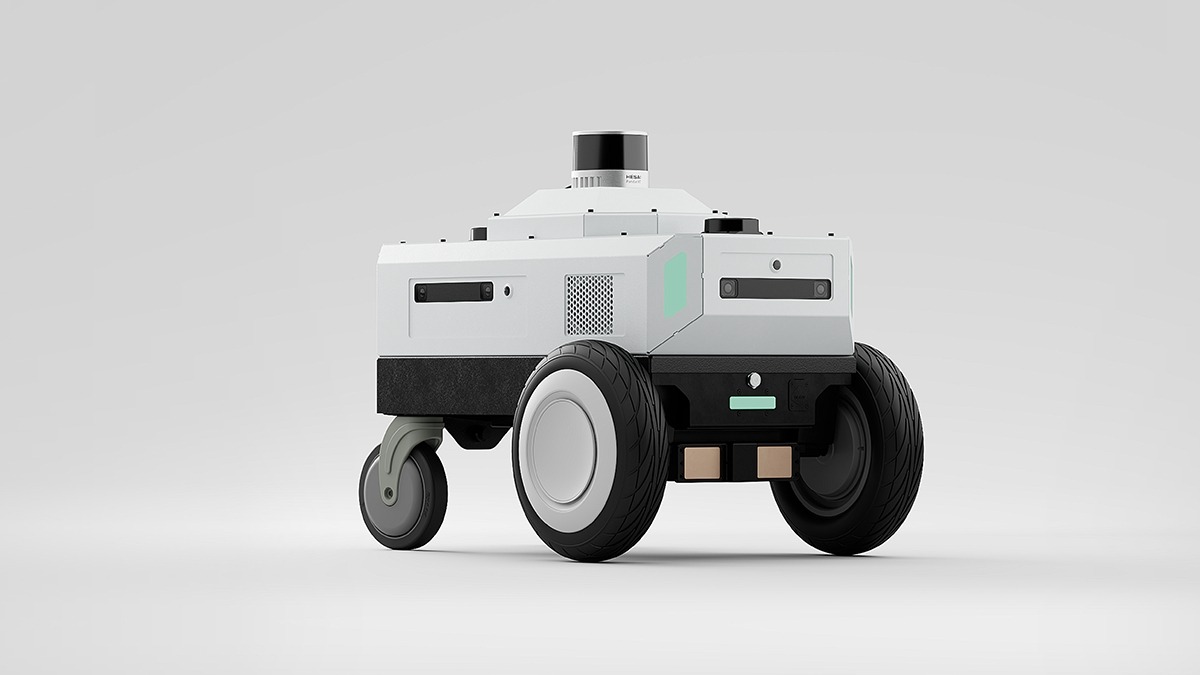
PAIN POINTS
Navigation Challenges in Complex Environments
In dynamic and cluttered factory settings, Autonomous Mobile Robots (AMRs) face significant challenges in avoiding collisions with other robots, human workers, or unexpected obstacles. The presence of moving equipment, pedestrians, and constantly shifting environments makes it difficult for AMRs to navigate efficiently without risking accidents or delays. This requires precise and reliable navigation systems to ensure safety and operational continuity.
HESAI SOLUTION
High-Precision Navigation in Complex Environments
XT32 delivers highly detailed 3D scanning with centimeter-level precision, enabling Nova Carter to safely detect and navigate around obstacles. In dynamic warehouse settings filled with racks and moving objects, the XT32's 360° horizontal field of view ensures accurate obstacle detection, collision avoidance, and optimal path selection for seamless operations.
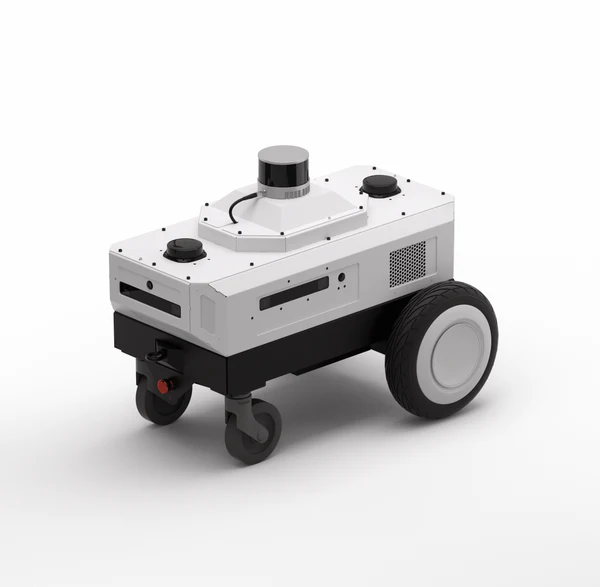
PAIN POINTS
Inadequate Close-Range Performance
AMRs often encounter difficulties when navigating tight spaces, such as narrow aisles, storage racks, or areas with densely packed equipment. These close-range environments demand highly accurate sensors that can detect objects in immediate proximity to the robot, allowing it to maneuver safely and avoid collisions. Without the ability to reliably perceive objects at short distances, AMRs risk operational inefficiency, slowdowns, or accidents in confined areas.
HESAI SOLUTION
High-Resolution with Zero Blind Spots
With a minimum range of zero, the XT32 can effectively detect objects even if they are directly touching the sensor’s enclosure. In factory environments, XT32 enables Nova Carter to safely operate in confined areas such as narrow aisles or loading zones, without the risk of undetected obstructions.
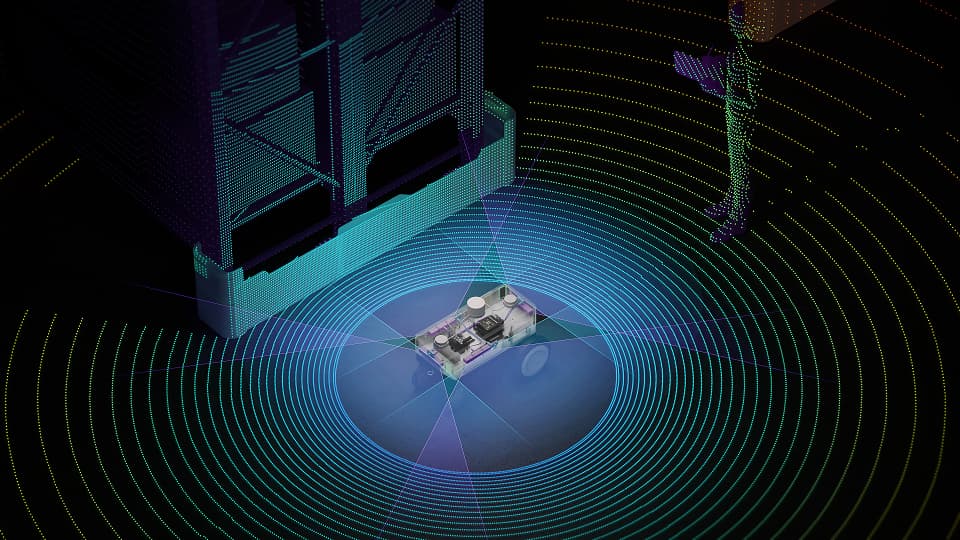
PAIN POINTS
Unreliable Performance in Challenging Weathers
AMR often faces challenges in maintaining consistent operation across diverse environments. Exposure to harsh weather, temperature fluctuations, or rugged terrains can lead to performance degradation and frequent maintenance, disrupting operational efficiency.
HESAI SOLUTION
Robust Reliability for All-Weather Operations
XT32 has passed over 50 reliability validation tests such as waterproof, dustproof, and mechanical shock. In outdoor applications where the Nova Carter may be exposed to varying temperatures or challenging weather conditions, the XT32’s robust reliability ensures AMR to operate without performance degradation.
DRIVING INNOVATION TOGETHER
Connecting with Industry Leaders
Hesai proudly partners with a diverse array of clients across industries, from pioneering startups to established industry leaders in robotics. Our collaborative network encompasses logistics giants, agricultural innovators, urban planners, and surveying experts, among others.
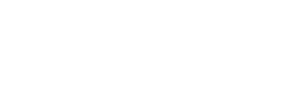
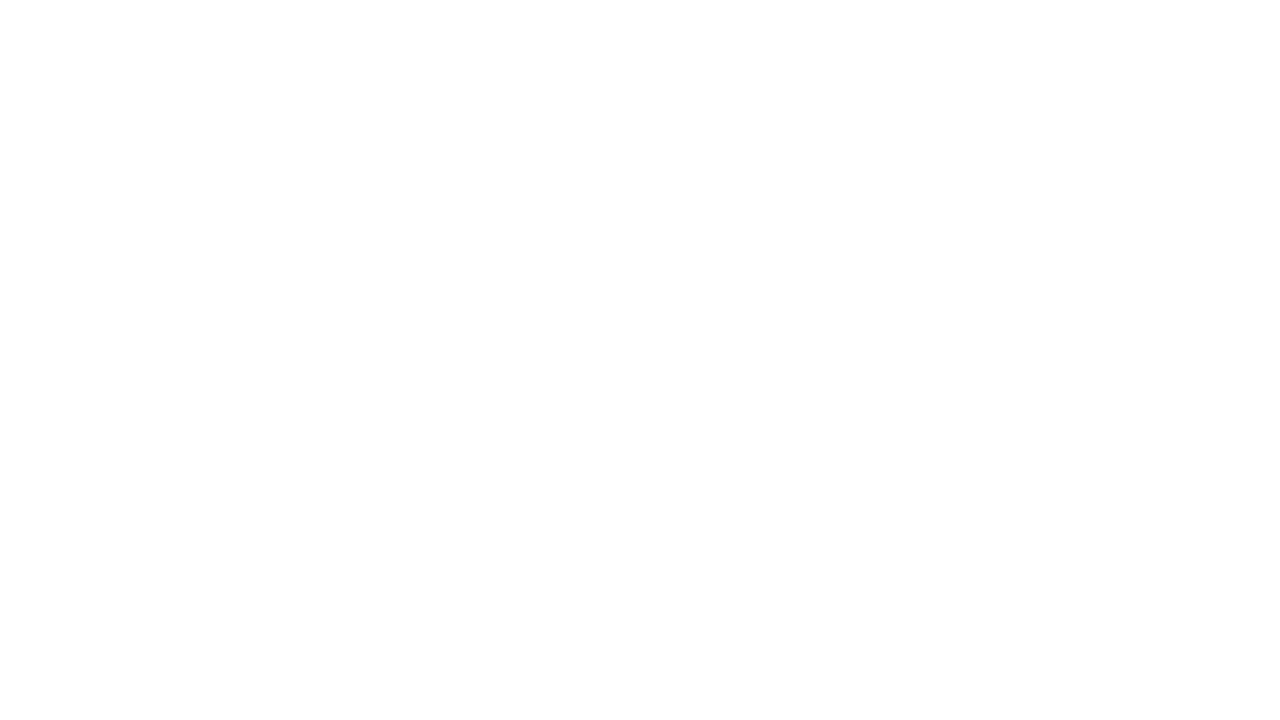
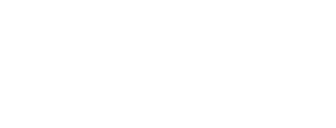
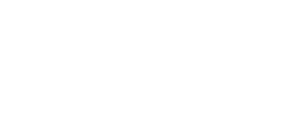
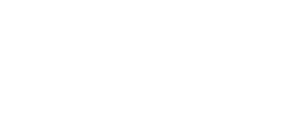
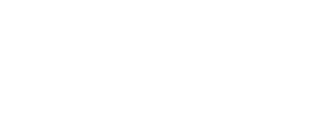
NEED EXPERT ASSISTANCE?
GET IN CONTACT
X
ACCESS DOWNLOADS NOW
Please fill in all fields
X
CONNECT WITH A LIDAR EXPERT TODAY
Connect with our sales team to explore how our cutting-edge technology can empower
your business today.