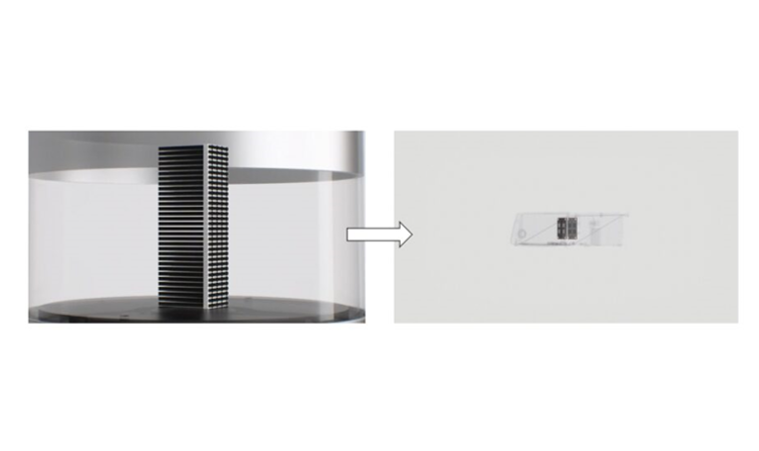
Lidar, relatively unknown to consumers just two years ago, has now gained recognition as a cutting-edge sensor for self-driving vehicles. The journey from a niche technology to widespread consumer adoption can be attributed to innovations in both its design and production process.
In 2016, automotive lidars were as bulky as coffee makers, with expensive models commanding prices as high as $75,000 USD – equivalent to the cost of a small apartment. Today, Hesai’s ultra-slim lidar is less than two fingers in height, while the price of long-range lidar has fallen to only 1% of its price from seven years ago, making lidar an affordable yet state-of-the-art technology that is now within reach of consumers.
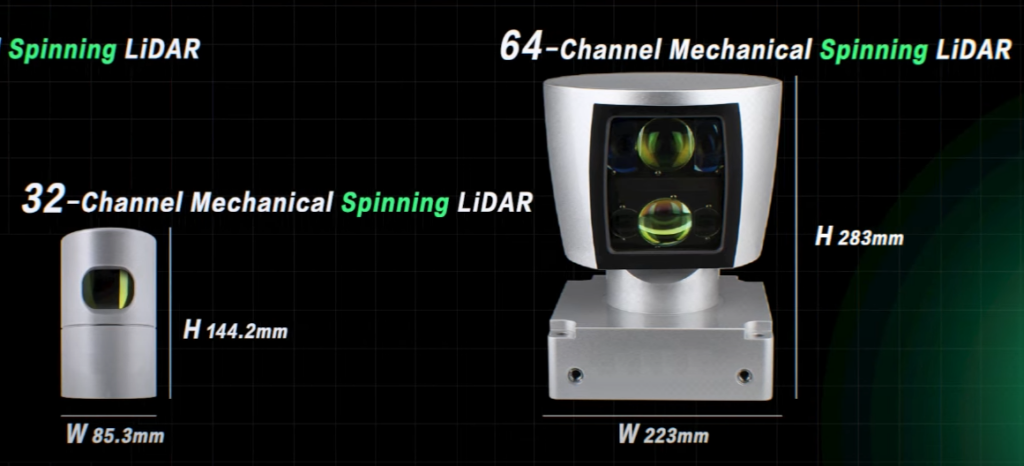
Conventional lidar resembles a coffee maker
Given its inherent performance advantages over other sensors, lidar’s increasing affordability has created unprecedented market opportunities. Auto Shanghai 2023 featured over forty passenger vehicles equipped with lidar. With further improvements and the adoption of assisted driving technology (ADAS), lidar is increasingly recognized as an essential hardware for delivering active vehicle safety.
Lidar overcame its challenges in size and cost through three key innovations: chip-based integration, a platform module design, and fully automated production lines.
Chip-based Design — The Number One Tool for Cost Reduction
Lidar senses its surroundings by emitting and receiving infrared laser beams. By calculating the time it takes for each beam to travel and return, it calculates the distance of each point in space. To achieve a detailed map of the surroundings, lidar needs to operate at a speed of millions of points per second.
Traditional lidars follow a discrete design, by stacking hundreds of separate laser channels, receivers, and processors together into one package. This results in a bulky structure with thousands of parts, requiring high levels of precision during the assembly process. As a result, conventional lidar not only occupies significant space but also comes with a high cost of production. Overcoming these limitations has been a major goal for the industry.
Application-specific integrated circuit (ASIC) technology offers a solution by integrating multiple discrete electronic components into a small semiconductor wafer. In the case of lidar, the chip-based approach integrates electronic components such as laser control circuits, signal acquisition and conversion circuits, and waveform-processing circuits into a few compact chips. This enables efficient control and operation of hundreds of laser channels within the space of a single microchip.
The chip-based design significantly reduces the number of components, leading to considerable cost reductions. The simplified architecture results in fewer assembly steps, improved optical alignment, and automated production, both reducing cost while improving performance.

The chip-based approach simplifies the design architecture and number of components in a lidar sensor.
Product Platforming Accelerates Mass Production
As more real-world applications adopt lidar technology, Hesai has broadened its offering from a single product into six main product lines with over ten standard products. A larger product portfolio requires better production systems. This includes effective management and design, iteration, and the development of final product lines. The design itself can have a large effect on production: products designed from scratch often fail to use shared technology or reuse material, and new products would require separate R&D, procurement, and production systems. To address these challenges, Hesai has adopted a modular and platform-based design that plays a key role in helping Hesai become the first lidar company to achieve mass production.
Platform-based design enables Hesai to develop products based on a shared product architecture while addressing a diverse set of requirements. The same lidar transceiver mechanism, which includes the key components that transmit and receive laser beams, can be combined with different scanning methods to develop new lidar products. For instance, combining the transceiver chip from the automotive-grade AT128 lidar with a 360° rotating platform creates a fully integrated 360° rotating lidar system. These rotating systems are ideal for L4 autonomous driving applications which require high levels of performance and a wider field of view.

Hesai embraced the platform-based design early on. Its Pandar series is available in 40, 64, and 128 channel options under the same architecture, while the XT series has 16 and 32 channel options. Lidars in the same series are consistent in their size and interface, making it easy for OEM customers to adopt newer models and to seamlessly switch between sensors.

Hesai’s complete lidar product line.
A modular design approach has helped Hesai achieve higher levels of uniformity across multiple product lines. In the AT and ET product families, 70% of the component architecture is shared, significantly reducing supply chain management costs. This approach allows for more effective usage of the core technology, creating even more competitive products.
Building an Automated Factory to Innovate and Reduce Manufacturing Costs
While the chip-based approach targets cost reduction at the product design phase, self-built automated production lines focus on reducing costs during the manufacturing phase. Lidar production has evolved from expensive and inefficient manual processes to cost-effective highly automated production.
Hesai has always emphasized production-oriented design. Its design choices—including the chip-based integration and modular platforms—make streamlined, automated manufacturing possible. Highly automated production lines are now in use for calibration, assembly, and testing. Fully automated production enhances manufacturing stability, reduces quality issues, and lowers operating costs, transforming a time-consuming and labor-intensive step into a highly-efficient one.
Hesai’s production lines have an automation rate of over 90%
In addition, by building its own factory, Hesai maintains control over all production stages. In-house production enables Hesai to quickly optimize production processes to ensure high-quality and efficient mass-scale delivery. By integrating intelligent manufacturing technology, Hesai’s factory automates over 100 production processes with an automation rate of over 90%. The result: Hesai manufactures one lidar unit in just 45 seconds, much faster than traditional methods.
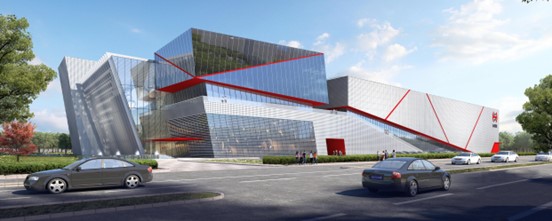
Hesai’s Maxwell intelligent manufacturing center
Conclusion
Hesai’s innovations have made lidar more affordable and accessible to its users, especially everyday consumers looking to buy cars with ADAS functionality. With its direct, stable, and accurate geospatial measurements, lidar enables ADAS software to quickly respond to challenging environments. Driving scenarios such as darkness and glare, as well as other situations, are easily solved by lidar whereas camera-based vision algorithms may fall short. The number of lidar-equipped vehicle models is steadily increasing across the board in both high-end and more affordable vehicle options. Increasing adoption will continue the positive feedback loop of supply and demand, strengthening the supply chain and further reducing production costs.

Hesai’s currently announced OEM partners.
Hesai’s commitment to making lidar more effective and more accessible has solidified its position as a leader in the global market. With over 135,000 lidar units delivered to date – Hesai’s product output is higher than all U.S publicly listed competitors combined. With its chip-based design, modular platform, and automated production, Hesai has demonstrated its capability to reduce costs at scale, positioning it for a bright future to launch the next generation of high-performance lidar sensors.